How business can help fashion supply chains decarbonize
If fashion brands are serious about slashing emissions, they must start with their suppliers, which need a lot of support. The post How business can help fashion supply chains decarbonize appeared first on Trellis.
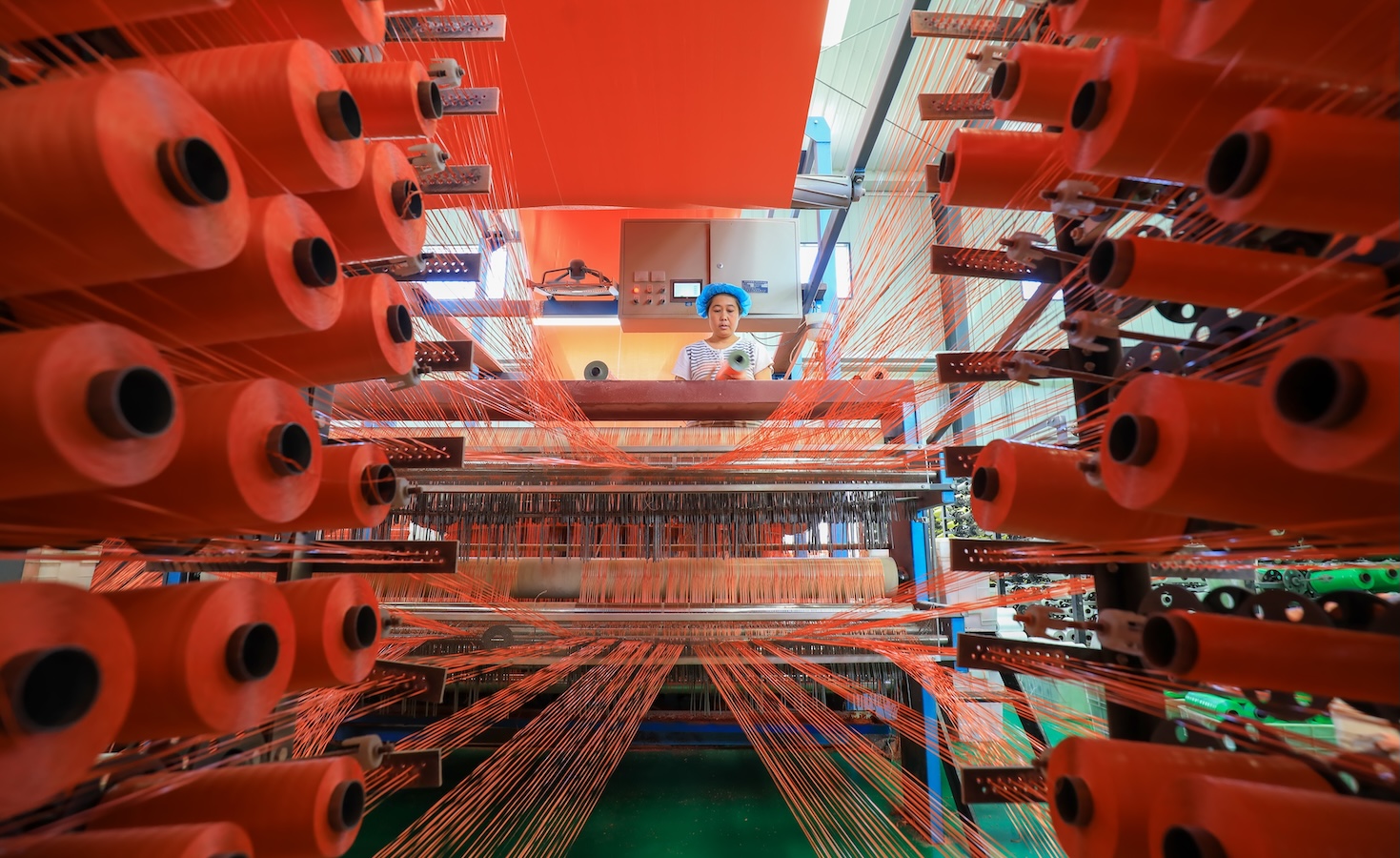
H&M is joining the Apparel Impact Institute (AII) in rallying brands, textile companies and banks to rid fashion supply chains of fossil fuels. The technologies are ready, they contend, and the payoff is huge for companies and the climate. However, thousands of yarn spinners, textile makers and garment processors in developing nations need more than mandates and advice from brands. What they really need, according to the AII, is cash.
That’s why the Oakland, California, nonprofit is calling on industry heavyweights to contribute $10 million each toward advancing its $250 million Fashion Climate Fund. H&M has already done so, and it wants more company.
The fund launched in 2022 to end the use of coal and natural gas among suppliers. Target and PVH have also each agreed to $10 million. HSBC Bank, H&M Foundation and the Schmidt Family Foundation committed, too.
The goal is to reach net zero by 2050 in footwear and apparel, drawing down emissions by 45 percent by 2030. That involves replacing fossil fuels by 2040 with low-carbon thermal energy sources such as industrial heat pumps, electric boilers and waterless dyeing. Ultimately, the industry needs $1 trillion from public and private sources to completely decarbonize, according to the AII.
More than 70 percent of the fashion industry’s emissions come from producing and processing materials, according to McKinsey. However, tension exists between apparel brands (asking suppliers to reduce that footprint) and often-less-powerful suppliers (scrambling to make retrofits on small budgets).
“”A significant proportion of textile suppliers are small and medium-sized enterprises that struggle with their cash flow, aren’t considered creditworthy and don’t have access to loans,” said Lewis Perkins, president of the AII. “This is where brands must lead, offering direct funding, co-investment models, and facilitating access to affordable financing solutions.”
Lessons from India
Arvind Group is a leading denim manufacturer in India. Its head of sustainability, Abhishek Bansal, described a recent partnership with H&M on supercritical CO2-based dyeing for cotton and polyester-cotton blends. “We both have come together to make this technology commercially established, commercially viable and put it out as an example to the industry,” he said in a recent online press event.
H&M provided the upfront financing, helping to reduce thermal energy demand in Arvind’s operations by more than 70 percent, according to Bansal.
“One thing that I often hear from other brands when I talk directly to them is, ‘How did you get your CFO, or how did you get your treasury to buy in on this?’” said Kim Hellström, senior sustainability lead at H&M, of teaming up with suppliers. “It kind of goes back to how serious are you. Is it an honest target? Is your climate target honest? Are you doing everything to reach it?”
The best way for companies to support cleaner energy in suppliers’ factories, he added, is to build the cost into the price they pay for goods from those suppliers.
“We don’t need to talk about innovation,” Hellström said. “Heat pump technology is super efficient. It has been around for decades. Heat storage is exploding. There are different types of material for this. There’s molten salt, there’s sand, there’s bricks. There are many different technologies that can help with electrification.”
The institute’s latest report, “Low-Carbon Thermal Energy Roadmap for the Textile Industry,” released March 11, provided granular details about what it would take to decarbonize “a typical wet-processing textile plant” in China, India, Vietnam, Bangladesh or Indonesia. It’s specific to the energy- and water-intensive operations that dye, wash, bleach or finish fabrics and garments, but the findings also apply to energy at other types of apparel plants.
“There are not some technologies in the future,” said Ali Hasanbeigi, founder and CEO of research firm Global Efficiency Intelligence. “You can go buy them today.” If steel plants can do power purchase agreements, he added, then so can relatively tiny textile plants.
“We have to figure out the cost and financing and matching different stakeholders,” Hasanbeigi said. “We need pilots. We need first movers.”
The AII’s model for collective action seeks to overcome some hurdles involved in aligning multiple players behind a common goal. “We kind of ruthlessly prioritize and identify the stakeholders that we know can bring impact,” said Climate Portfolio Director Pauline Op de Beeck, based in Amsterdam.
Seven strategies
The AII offered seven ways for large corporations to help their suppliers adopt thermal energy and electrify:
- Provide financial support: Offer direct financial assistance to suppliers through grants, flexible investment programs and premium pricing to offset the upfront costs of retrofitting low-carbon technologies.
- Support first-mover projects, especially in the next five years. Pilot efforts may include industrial heat pumps, electric boilers and waterless dyeing techniques.
- Commit to renewable electricity procurement: Develop long-term roadmaps for transitioning, particularly in countries such as India with emerging renewable infrastructure.
- Collaborate on technical solutions: Work closely with suppliers to reduce thermal energy loads and test innovative technologies such as waterless dyeing. Companies should also share risks and costs.
- Signal demand in the market: Develop consistent commitments for low-carbon technologies to build long-term relationships, and confidence for suppliers.
- Focus on energy efficiency: Start with the usual low-hanging fruit to reduce electrical demand in the first place. This makes an energy transition more affordable.
- Advocate for policies: Support helpful regulatory infrastructure for renewable energy procurement in key manufacturing countries. Bangladesh and India may need special attention.
Meanwhile, the AII is working with the nonprofit Cascale to develop an Industry Carbon and Energy Benchmark that would help to build a long-term business case for net zero facilities in apparel. In September, the two groups plan to engage the top 1,500 emitters in the industry to tackle climate solutions.
[Join over 1,500 professionals transforming how we make, sell, and circulate products at Circularity, April 29-May 1, Denver.]
The post How business can help fashion supply chains decarbonize appeared first on Trellis.